Clean Sky 2 aims to deliver full-scale in-flight demonstration of novel architectures and configurations in order to enable step-changes in environmental and economic performance and bring crucial competitiveness benefits to European industry. Aircraft level objectives of greening, mobility improvement, fulfilment of future market requirements and contribution to growth cannot be met without strong progress on the airframe. On greening, for example, the ambitious CO2 and noise reduction targets of FP2050 may rely for between 30 and 50% on progress on airframe.
Heat and fire cause more damage on composites than on metallic materials. In order to improve the current epoxy based composites behaviour under thermal affection, a new alternative is going be addressed: thermoplastic composites. In addition, the sector is making a transition to a more efficient aircraft, increasing the thermal resistance of the structures as well as reduce the number of heat & fire sources.
Hence, there are several reasons behind the drastic shift from aluminium and steel to composites: weight reduction, better fuel economy and lower operation costs, emissions reduction, corrosion and fatigue resistance or, in some cases, flame resistance. The framework of this topic is AIRFRAME ITD Work Package B-2.1 and B-2.2 whose objective is to achieve lighter and more cost effective structures. In this line, current tendency at A/C level is to increase the structural contribution of the more efficient composites substituting metallic structures, developing fuselages with optimized usage of volume and minimized weight, cost and environmental impact.
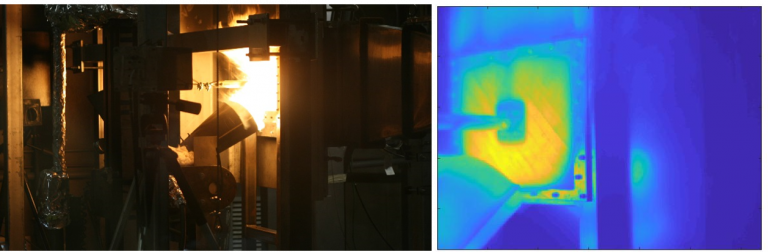
Under this framework, the research project HITCOMP aims to characterize the behaviour, under fire and thermal affection, of new high performance thermoplastic composites based on PAEK family resins, for comparison to the current thermoset, epoxy based, composites. HITCOMP aims as well to establish an innovative methodology allowing an affordable characterization of thermoplastics and the prediction of their behaviour and resistence when submitted to fire or high temperature events and to mechanical load. For this purpose, a thermo-mechanical model based on FEM permitting an innovative “virtual” characterization of specimens will be developed. An innovative testing lab based on two co-registrated IR cameras will be developed too. It will allow accurate, non-intrusive measurements of the actual temperature of both sides of the samples during the fire tests and for the adjustment and validation of the model.
LIR-Infrared Lab is as involved in the HITCOMP project in the role of project coordinator and in charge of thermal characterization of the thermoplastic composites. Two other companies are involved in the project: Sensia Solutions in charge of infrared imaging system and Instituto Nacional de Técnica Aeroespacial (INTA) in charge of materials manufacturing and mechanical characterization.
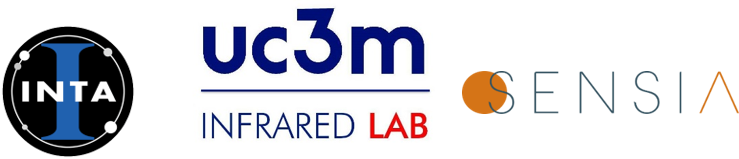